Dampflokomotive 11
[ vorherige Seite ]
[ previous page ]
Im November 2009 erteilte der Denkmalschutz die Genehmigung zur
betriebsfähigen Aufarbeitung der unter Denkmalschutz stehenden Lok
11.
Erste kleinere Bauteile wurden daraufhin abgebaut und auch schon
Aufgearbeitet (Ventile, Injektoren etc.).
Die Demontage der Großteile mit unserem Kran konnte nur im Freien
geschehen, aber ein halber Meter Schnee und eisige Temperaturen erlaubten
dies Anfangs noch nicht.
Über den Fortgang der Arbeiten werde ich von Zeit zu Zeit
berichten.
Februar 2010
Ende Februar war der Schnee abgetaut und es trafen sich einige Aktive an
mehreren Tagen hintereinander, um die Zerlegung der Lok in ihre Großteile
in Angriff zu nehmen. Nach knapp 50-jähriger Abstellzeit, die meiste
Zeit im Freien, mußten viele Verbindungen mit der 'Schlauchschere'
oder dem Trennschleifer getrennt werden.
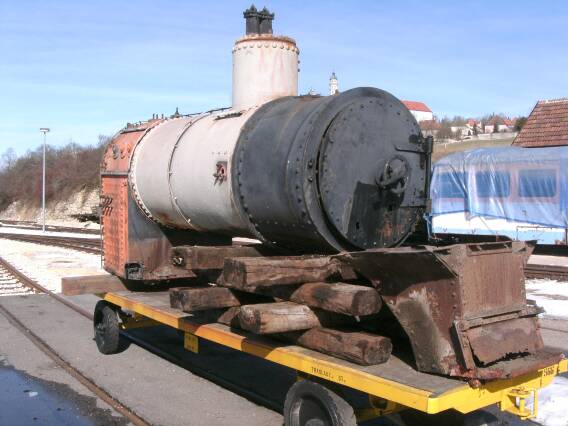 |
Der Kessel wurde auf den Wagen gestellt, der auch
schon den Kessel der Schwesterlokomotive 12 im Rahmen der
Hauptuntersuchung trug.
Vor dem Kessel liegt der Aschkasten. |
Das Fahrgestell trägt hier nur noch den
Wasserkasten und die Zylinderblöcke samt Kesselauflager, sowie
diverse Kleinteile wie Zug- und Stoßvorrichtung, Trittbretter etc. |
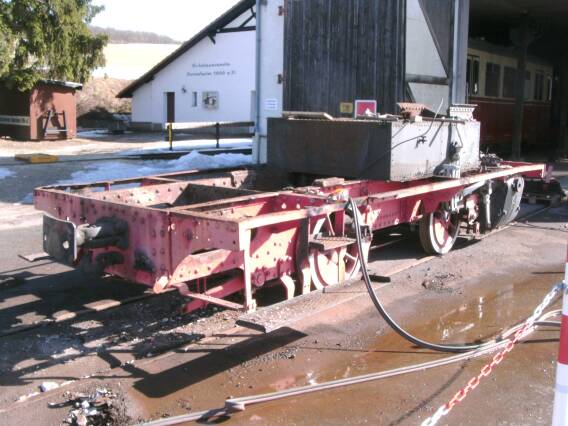 |
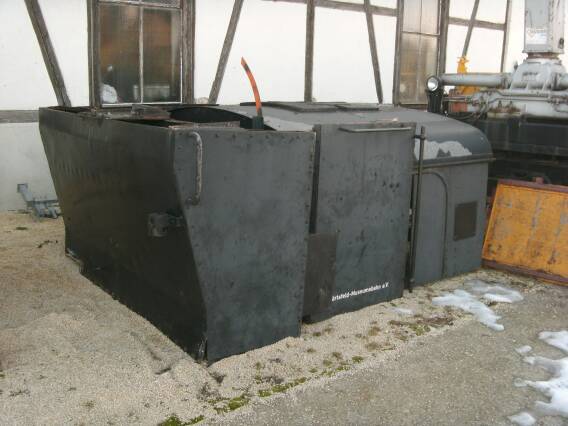 |
Führerhaus und Kohlenkasten werden neben dem
Lokschuppen zwischengelagert. Mal sehen, welche Teile noch brauchbar
sind, und welche neu angefertigt werden müssen. |
Der Kessel ist noch der originale Kessel von 1913. Vor
allem die Feuerbüchse befindet sich auf den ersten Blick noch in
erstaunlich gutem Zustand. |
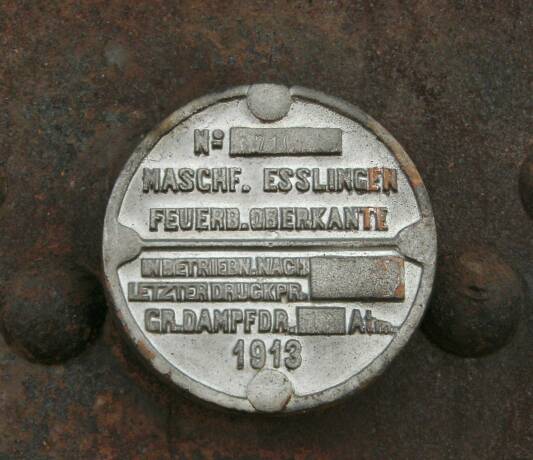 |
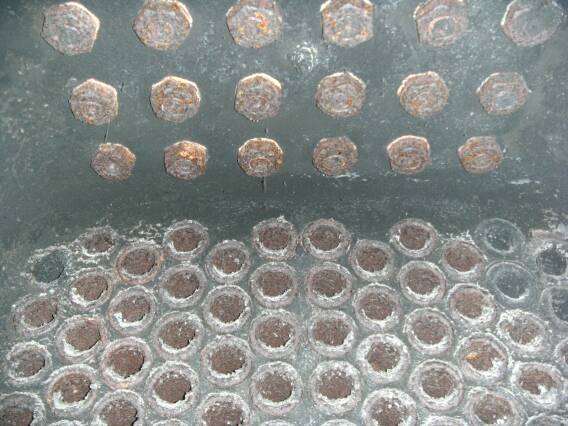 |
Auch der Blick in die Feuerbüchse auf die
Deckenanker und die Rohrwand zeigte keine offensichtlichen Schäden.
Die Rohre selbst werden aber sicher nicht mehr zu gebrauchen sein. |
Ob die Stehbolzen wohl noch in Ordnung sind? |
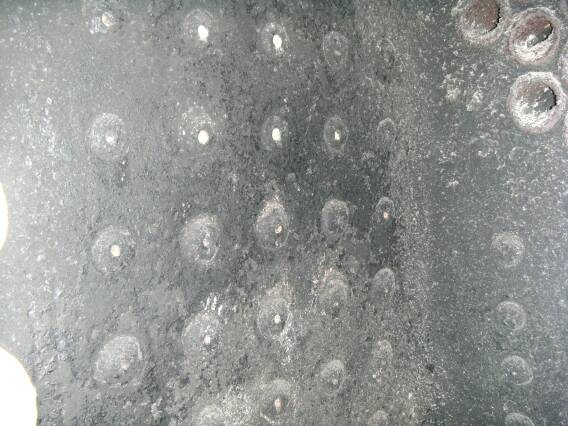 |
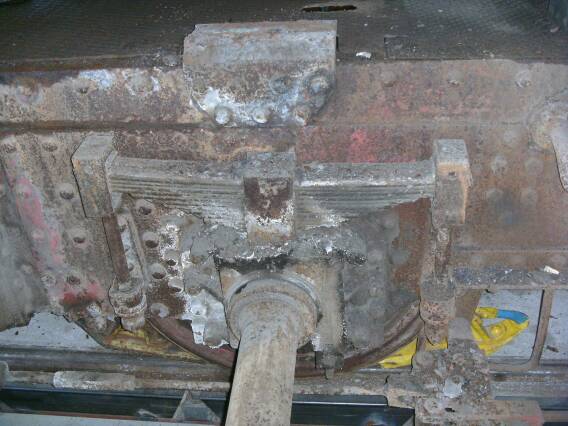 |
Ein Blick auf die Federung und das Achslager der
Hinterachse, der Winkel darüber trägt den Kessel. |
Die diversen Treib-, Kuppel- und Steuerstangen müssen
noch auf Risse geprüft werden, bevor sie wieder verwendet werden können. |
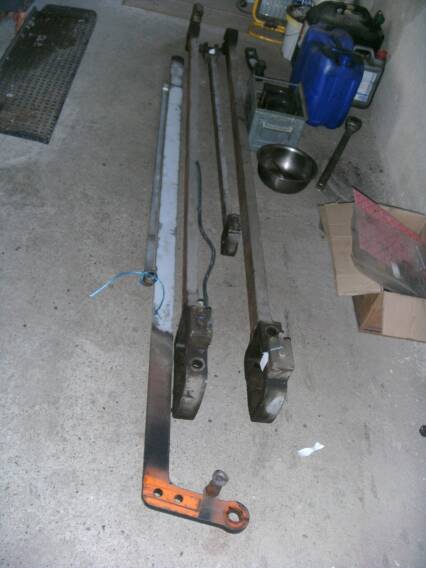 |
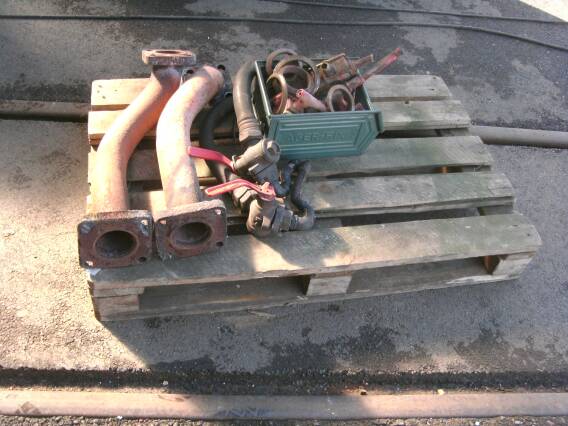 |
Abgebaute Kleinteile werden in Kisten und auf Paletten
gesammelt und in der Werkstatt aufgearbeitet. |
Die Klappe des Aschkastens ist gewaltig abgezehrt,
aber die Gelenke ließen sich erstaunlicherweise noch problemlos
bewegen.. |
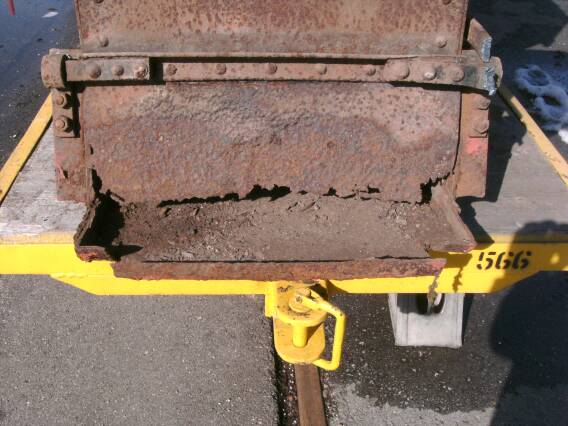 |
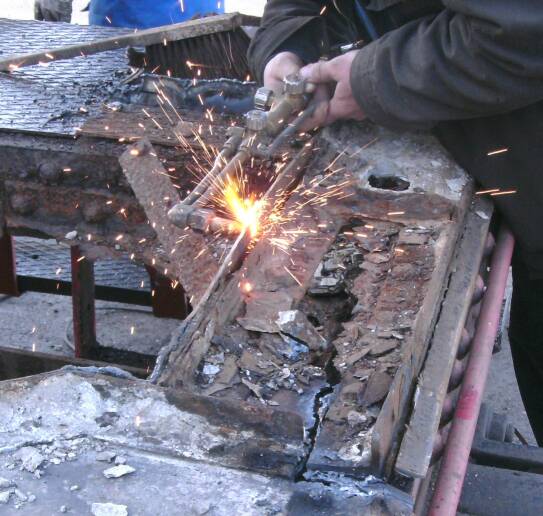 |
Die Reste des durchgerosteten Kohlenkastens mußten
mit dem Schneidbrenner zerlegt werden. |
In diesem Bereich ist auch der Rahmen der Lokomotive
so stark korrodiert, das einige der Bleche nicht mehr zu retten sind und
ersetzt werden müssen. |
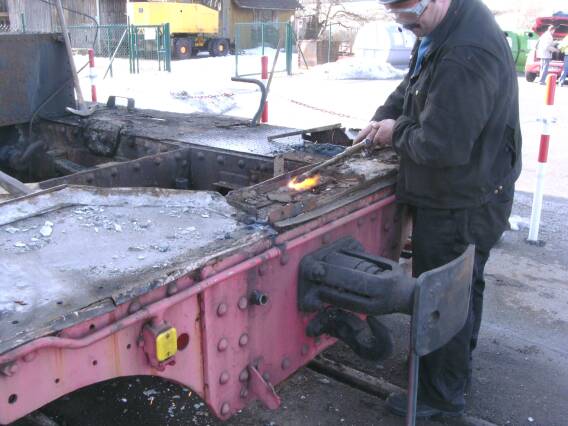 |
Die Arbeiten an der Lok 11 gingen weiter, in erster Linie zerlegen
und Bestandsaufnahme. Einige Teile wurden auch schon einer Rißprüfung
unterzogen, als der Sachverständige zur Kesselprüfung der
Schwesterlok 12 da war.
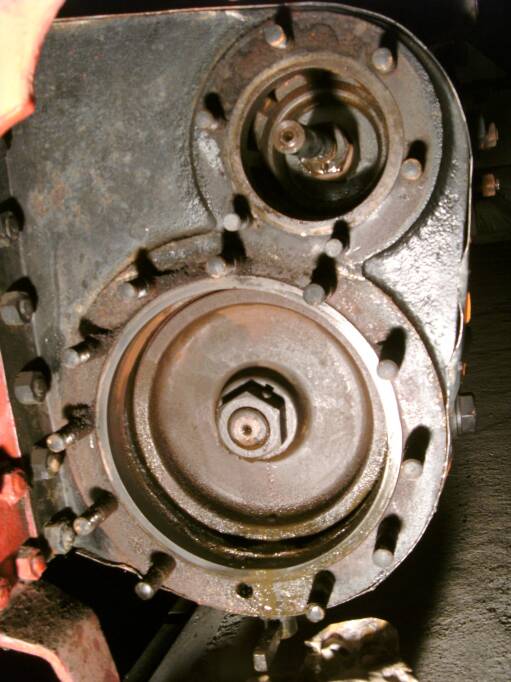 |
Nach dem Entfernen der Deckel von Dampf- und
Steuerzylinder zeigte sich das Innenleben in erstaunlich gutem Zustand.
Schließlich wurden die Zylinder seit mindestens 50 Jahren nicht
mehr geöffnet, wir haben allerdings regelmässing, wenn die Lok
bewegt wurde, Öl in die Zylinder gegeben. |
Die Lok wurde ausgeachst und auf ein Hilfsfahrgestell
gesetzt, um sie bei bei Bedarf leicht verschieben zu können und den
Rahmen auf einer annehmbaren Arbeitshöhe zu haben. |
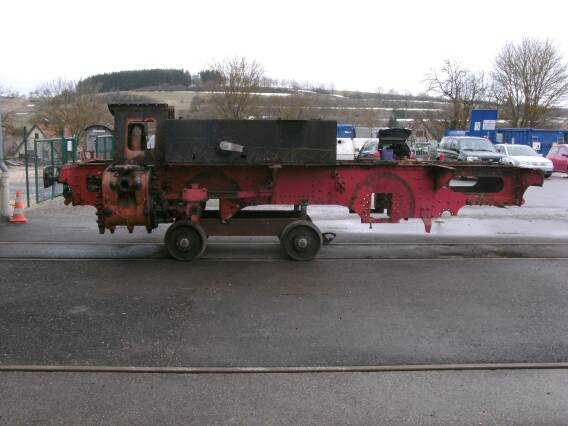 |
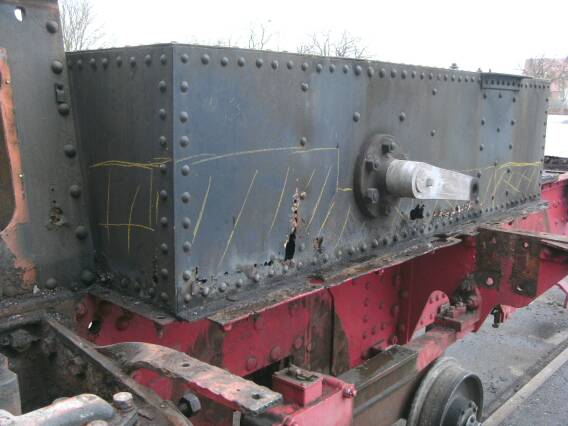 |
Der Wasserkasten sieht böse aus.... |
... aber auch der Rahmen hat in der langen Abstellzeit
gelitten, die Blechfragmente hier waren einmal 12 mm stark |
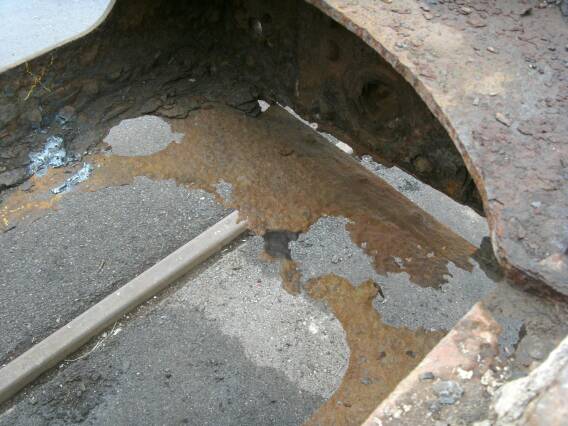 |
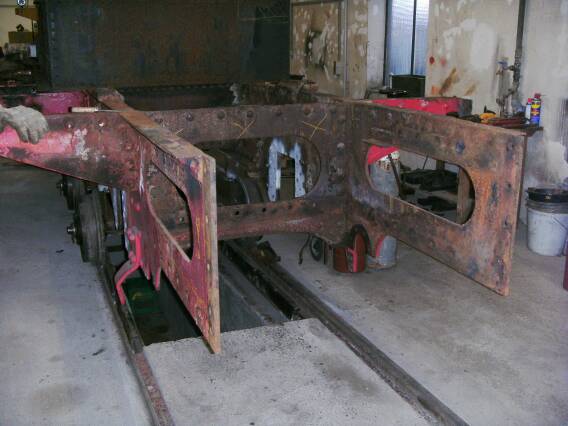 |
Die hintere Pufferbohle ist hier demontiert, um die
defekten Bleche ersetzen zu können. |
Auch hier am Längsträger hat die Korrosion
die Blechstärke an manchen Stellen von 15 mm auf 2 mm
reduziert. Dieser Teil wird abgetrennt, neu angefertigt und von einem
autorisierten Schweißer wieder angesetzt. |
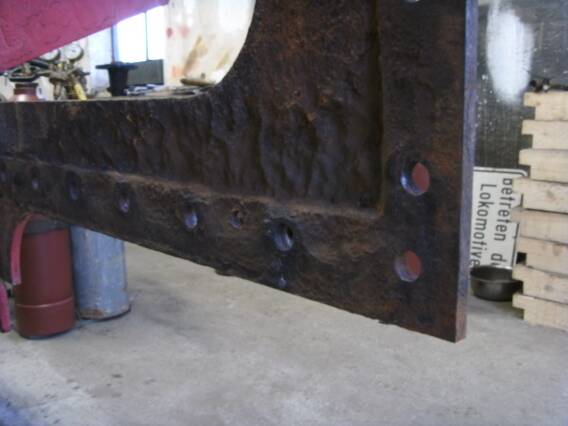 |
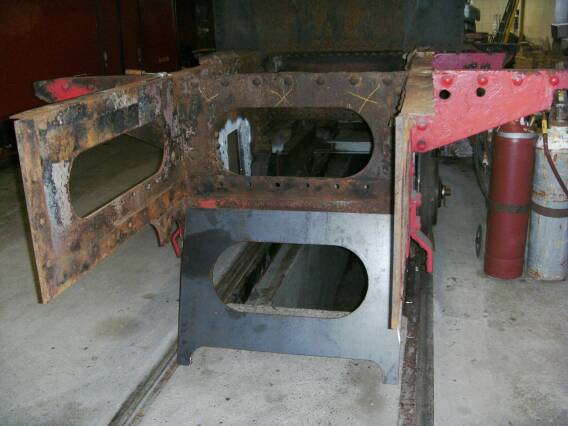 |
Dieses Querblech ist ebenfalls als zu ersetzen
markiert, das neue liegt schon zur Anprobe bereit. Alle Verbindungen,
die genietet sind, werden übrignes auch wieder genietet. Schweißungen
werden nur vorgenommen, wo Träger nur teilweise ersetzt werden oder
um Rostnarben aufzuschweissen, damit die zu nietenden Flächen
vollflächig und plan aufeinander liegen. |
Um den Kreuzkopf von der Kolbenstange zu trennen, müssen
wir diesen erwärmen und die Kolbenstange mit einem speziellen
Werkzeug auspressen. |
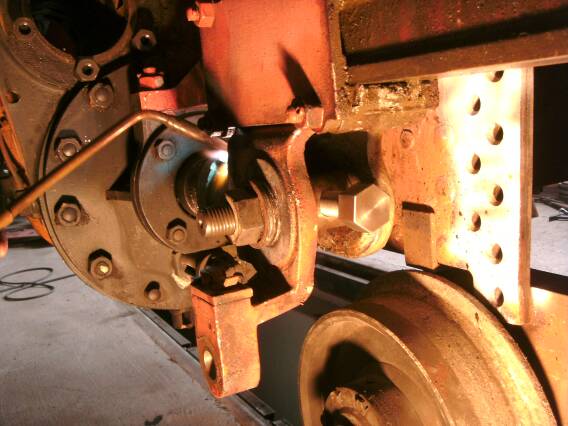 |
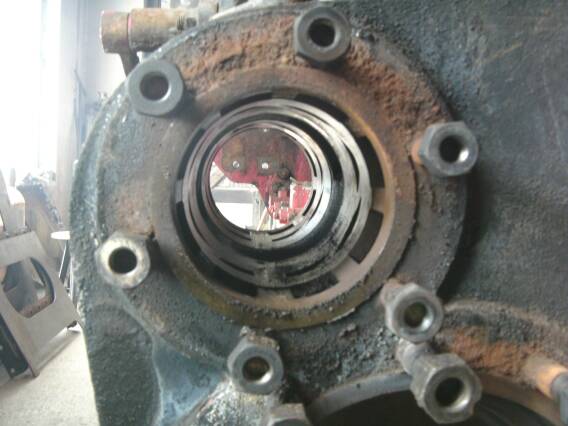 |
Ein tiefer Blick in den Steuerzylinder. |
Die Arbeiten am Rahmen der Lok gingen weiter
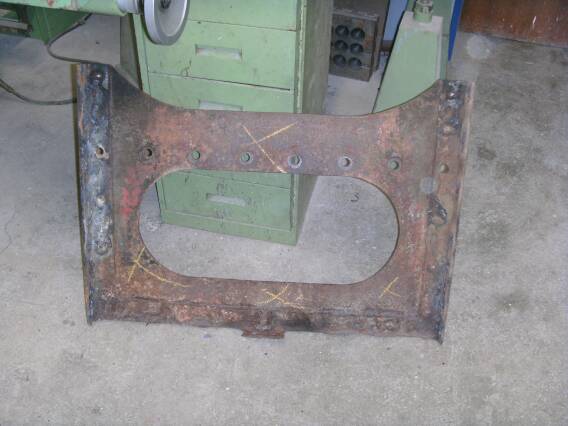 |
Das Querblech im Rahmen ist samt seiner Winkel derart
abgezehrt, daß es erneuert werden muß. |
Das neue Blech und die Winkel wurden geheftet und
werden gemeinsam gebohrt. |
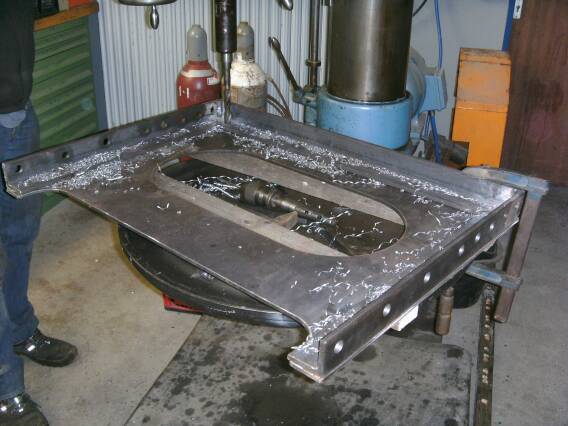 |
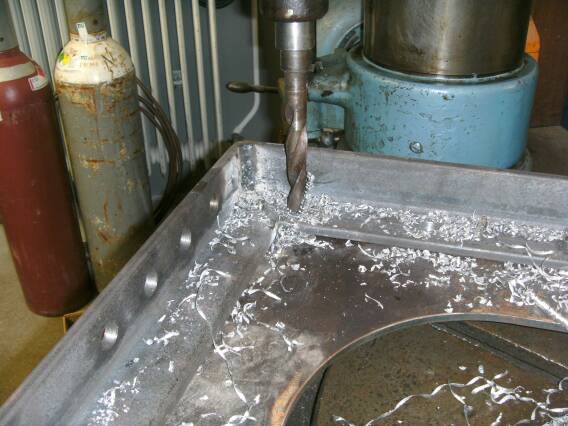 |
Nach dem Vorbohren werden die Löcher auf 20mm
aufgebohrt.. |
Der Bohrer in Aktion. |
 |
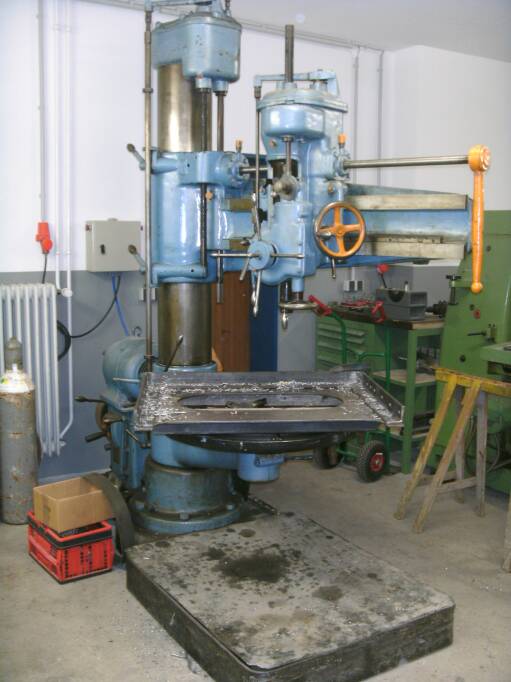 |
Mit diesem Bohrwerk werden die Rahmenteile der Lok
gebohrt Der Bohrtisch trägt alles was wir mit vier Mann drauf
wuchten können. |
Der Längsträger ist hier bis auf 2mm
Materialstärke abgezehrt. Da kann man nichts mehr Aufschweissen,
... |
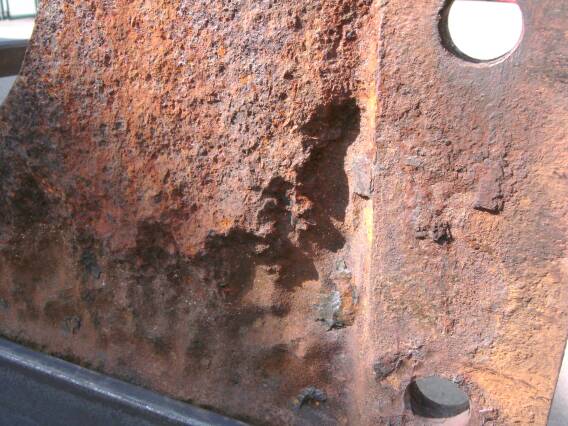 |
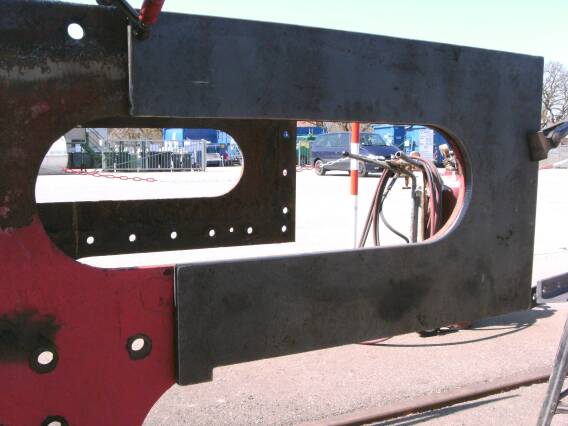 |
... da müssen neue Teile angepasst werden. Hier
werden gerade die alten Nietlöcher auf die Neuteile übertragen. |
Die Halter für die Blattfedern wurden auf Risse
geprüft, sandgestrahlt und sind schon fertig lackiert. |
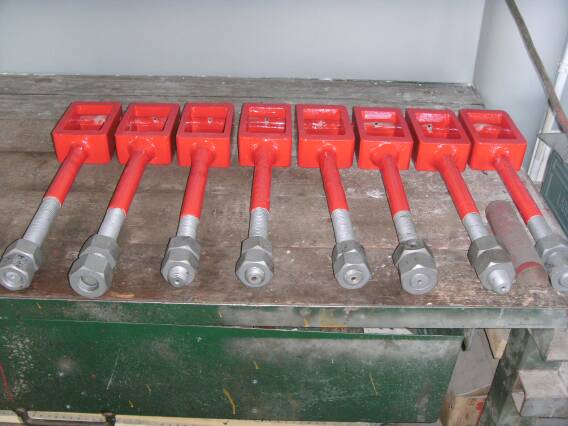 |
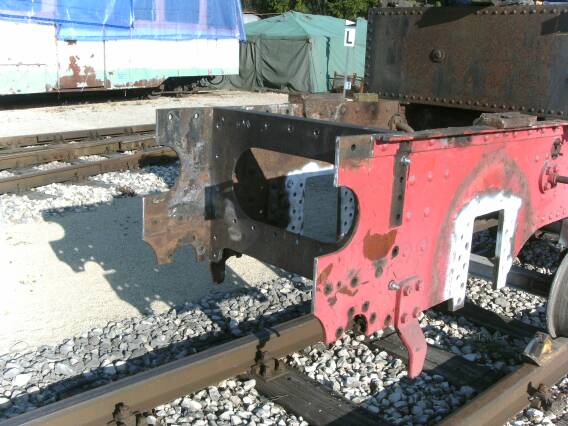 |
Die maroden Rahmenteile wurden kurzerhand
abgeschnitten. Der weiße Farbauftrag in den Achslagerausschnitten
ist keine Grundierung, sondern die Markierfarbe von der Rißprüfung. |
Dann wurden die neuen Rahmenteile von einem
entsprechend berechtigten Schweisser an den alten Rahmen geschweisst.
Das Grundblech der neuen Pufferbohle wurde mit ein paar Schweissraupen
an den vorbereiteten Verbindungswinkeln angeheftet. |
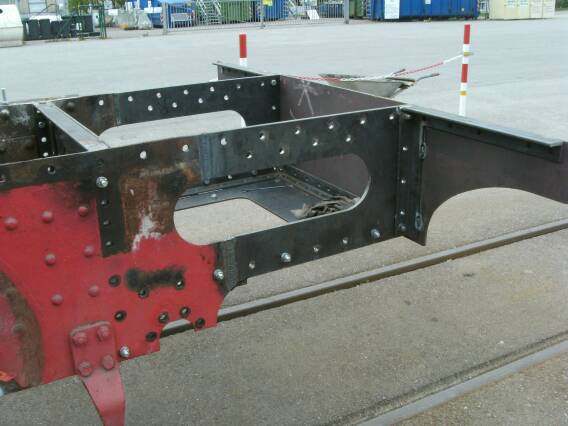 |
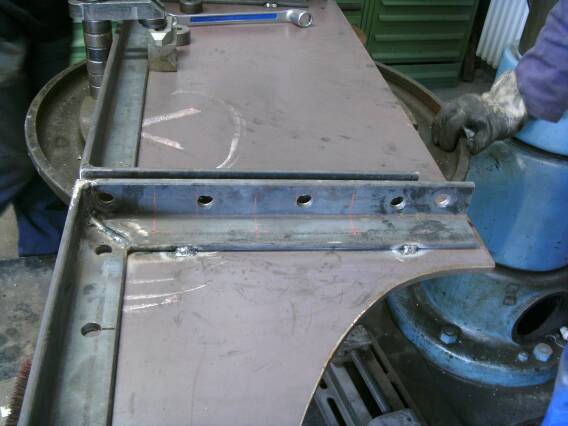 |
Dann konnte das Blech zum Bohren auf das Bohrwerk. |
Die Pufferbohle ist wieder montiert. Die
Dampflokmannschaft überlegt sich die Montageschritte des Verstärkungsblechs,
das die Zug- und Stoßkräfte von der Pufferbohle auf die Längsträger
übertragen soll. |
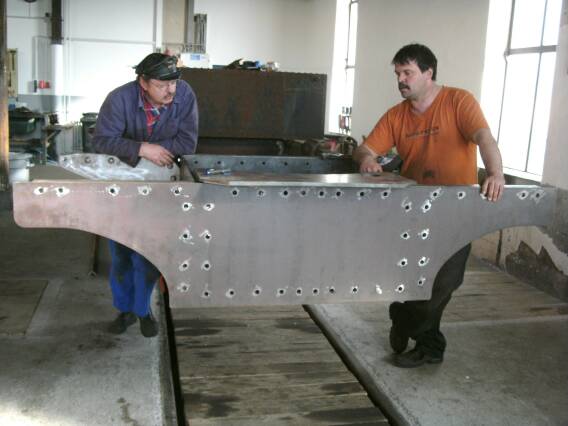 |
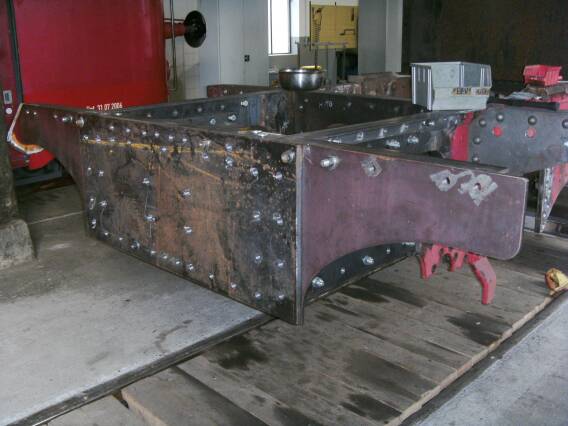 |
Die eingentliche Pufferplatte ist mit ein paar
Schrauben auf das Grundblech montiert. |
Diese Detailaufnahme zeigt die Stärkenverhältnisse
des 'dünnen' Grundblechs der Pufferbohle (12mm) und der wesentlich
stärkeren Pufferplatte. Dazu die Verbindungswinkel und der von
rechts einlaufende Längsträger. |
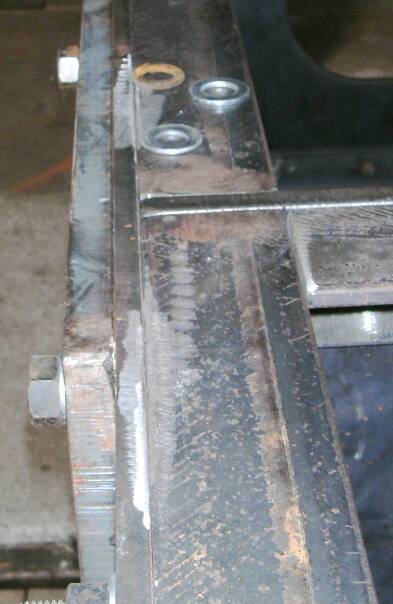 |
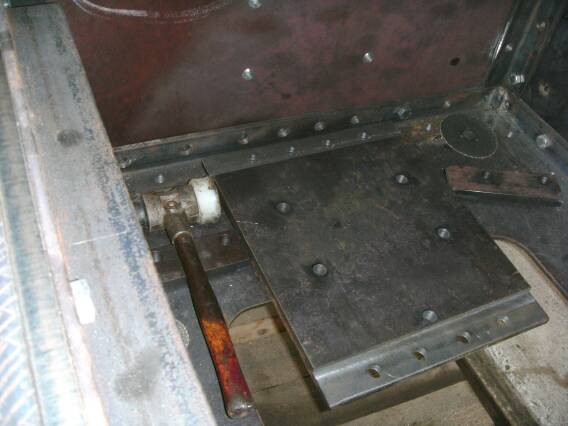 |
Auf die Rückseite der Pufferbohle wird im Bereich
der späteren Zug- und Stoßvorrichtungen noch eine weitere
Verstärkungsplatte angebracht. Diese ist an den Seiten ausgefräst,
um über die Verbindungswinkel greifen zu können. |
Der nächste Arbeitsschritt ist jetzt das Nieten der gesamten
Konstruktion. Überall, wo der alte Rahmen genietet war, wird auch der
neue Rahmen genietet. Und zwar richtig, keine Imitationen.
Die Nietaktion ist jetzt über die Bühne gegangen. Die
Entscheidung, den Rahmen zu nieten und nicht zu schweissen, fiel
einerseits, um die Originalität der Lokomotive zu wahren, und
andererseits, um diese alte Verbindungstechnik lebendig zu halten.
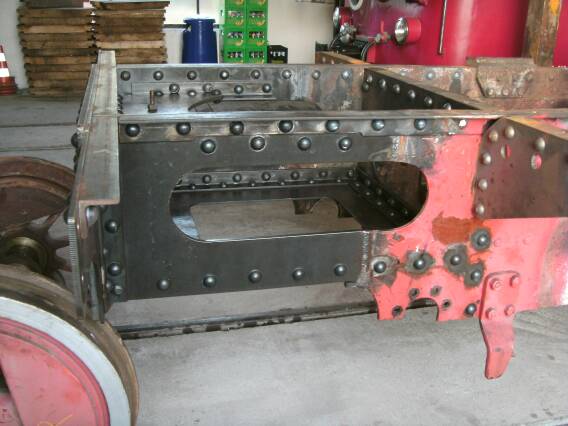 |
Blick von der Seite auf den neu angefertigten
Heckbereich der Lok. |
Der seitliche Träger des Führerhauses wurde
ebenfalls neu angefertigt. |
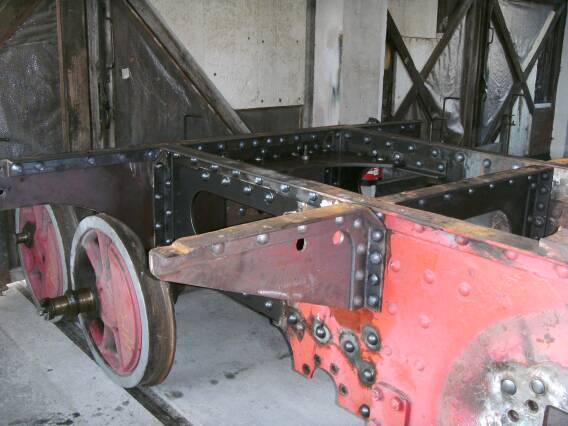 |
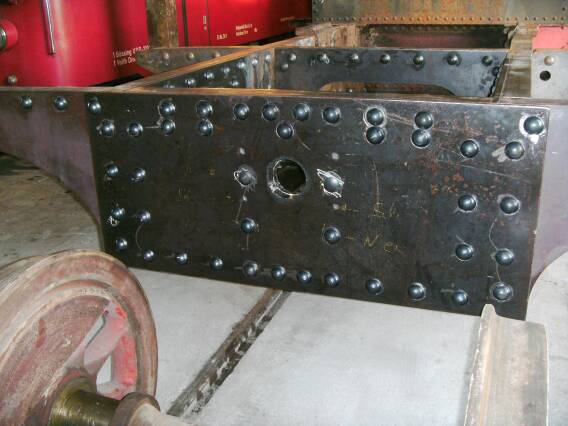 |
Die Pufferbohle mit ihren mehreren Lagen Material wird
mit besonders langen Nieten zusammengehalten. |
Die Innenseite der Pufferbohle zeigt die
Versteifungsbleche, welche die Zug- und Stoßkräfte der
Mittelpufferkupplung auf die beiden Längsträger einleiten. |
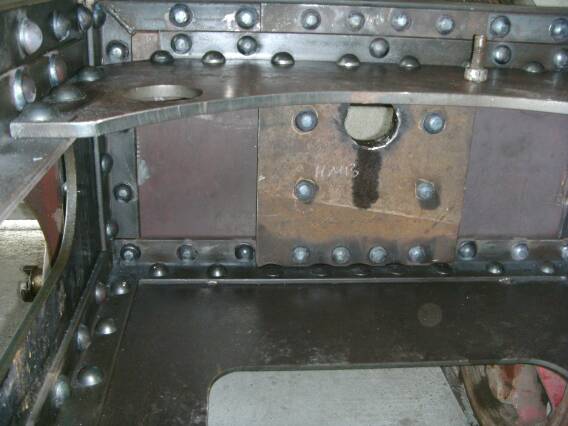 |
Die Übergänge von den alten zu den neuen
Rahmenblechen sind jetzt sauber verschliffen und ausgerundet, um keine
Kerbwirkung durch Kanten und Absätze zu haben. |
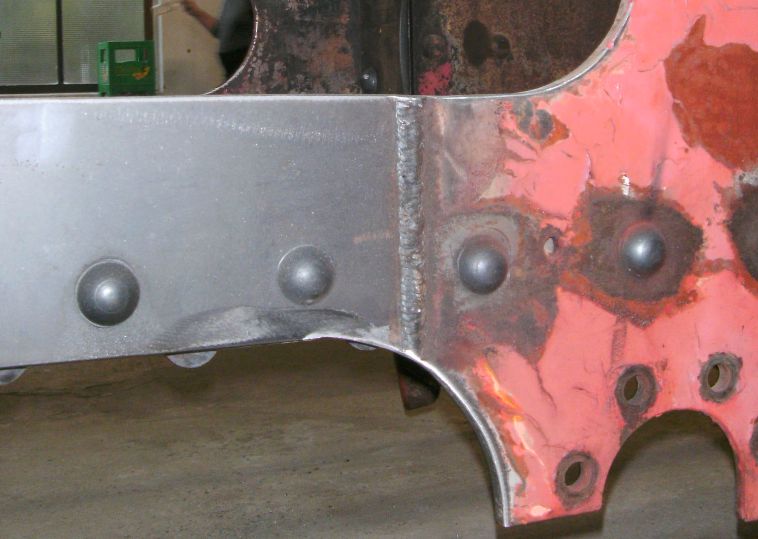 |
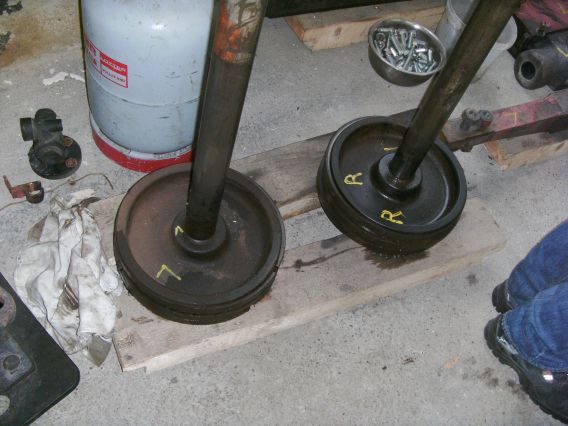 |
Die Kolbenstangen wurden von den Kreuzköpfen
getrennt und die Kolben ausgebaut. |
Die Radsätze der Lok waren beim Sandstrahlen und
Lackieren. Kaum zurück aus der Sandstrahlerei, wurden sie gleich
zum Abdrehen gebracht. |
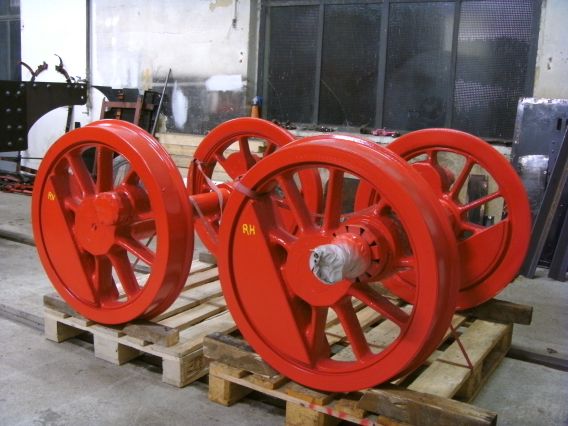 |
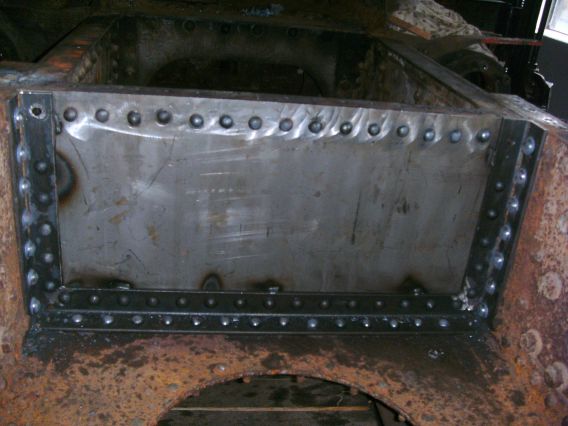 |
Das Oberteil des Wasserkastens wurde schon vor einiger
Zeit abgenommen, der untere Teil des Wasserkastens ist im Rahmen
integriert und das vordere Blech war stark abgezehrt und mußte
ersetzt werden. Die Seitenbleche am Rahmen und das Bodenblech mit dem
Mannloch sind noch in Ordnung und müssen nur entrostet werden. |
Der Wasserkasten wird von 12mm Nieten zusammengehalten. Im Gegensatz zu
den 20mm Nieten, die die Rahmenbleche verbinden sind diese schwieriger zu
verarbeiten, da sie aufgrund der geringeren Masse schnell auskühlen,
und zu heiß darf man sie ja nicht machen, da sie sonst verbrennen.
Wenn es bei den 12mm Nieten nicht auf Anhieb gelingt, den Gegenhalter zu
setzen, dann kann man sie gleich wieder rausnehmen, weil sie schon zu kalt
zum Nieten ist. Bei den dickeren Nieten hat man da etwas mehr Zeit.
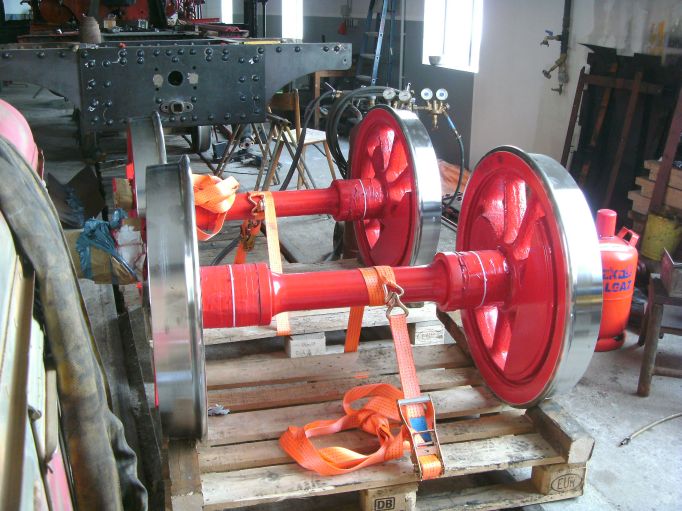 |
Nach einem Ausflug in den Harz sind die Radsätze
jetzt neu profiliert zurück in Neresheim.
Wenn der Lokrahmen (im Hintergrund) dann auch beim Sandstrahlen und
Lackieren war, können wir die Radsätze wieder einbauen. |
Die Radsätze sind natürlich gekennzeichnet,
nicht daß wir erst beider Montage der Treib- und Kuppelstangen
merken, daß die Radsätze vertauscht oder falsch herum
eingebaut sind. |
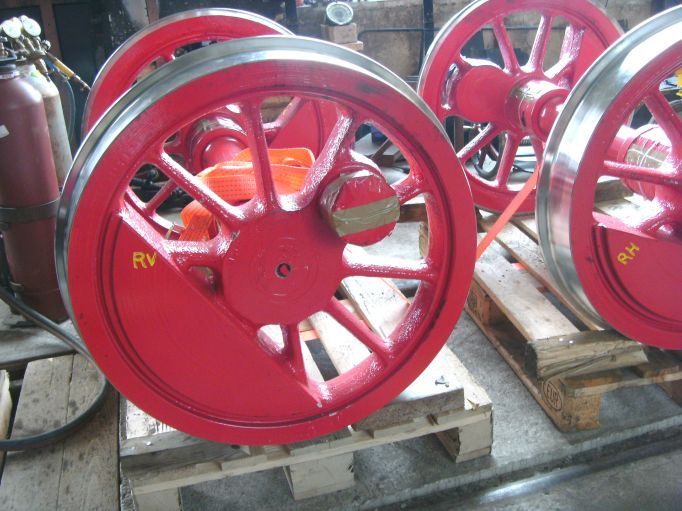 |
Hier noch ein paar Bilder vom Arbeitsablauf des Nietens.
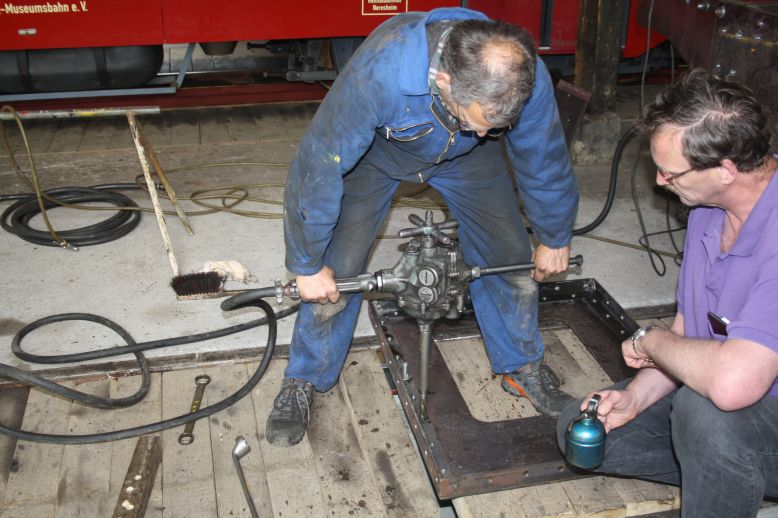
© 2010 Ingo Adam |
Zuerst müssen die Bohrlöcher auf das exakte
Maß aufgerieben werden. Die Bohrlöcher werden deshalb immer
einen halben Millimeter kleiner als das eigentliche Maß gebort,
damit auch geringe Ungenauigkeiten ausgeglichen werden können und
die Löcher exakt fluchten. |
Die Nieten werden in einem speziellen Brenner glüchend
gemacht. |
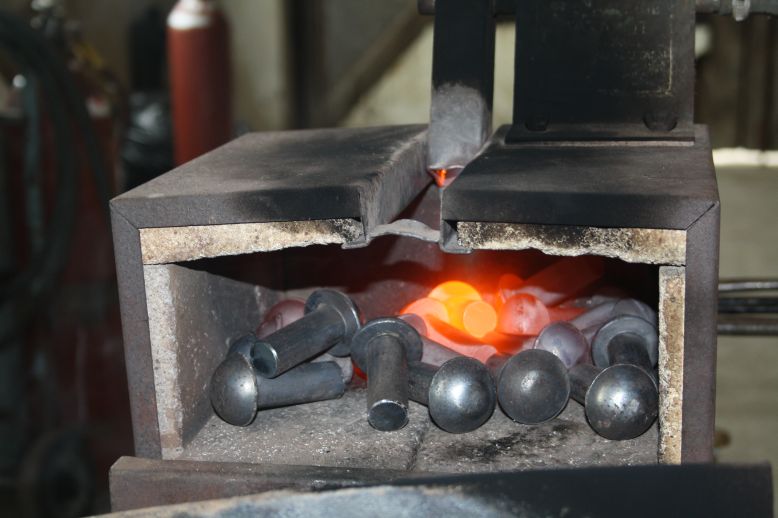
© 2010 Ingo Adam |
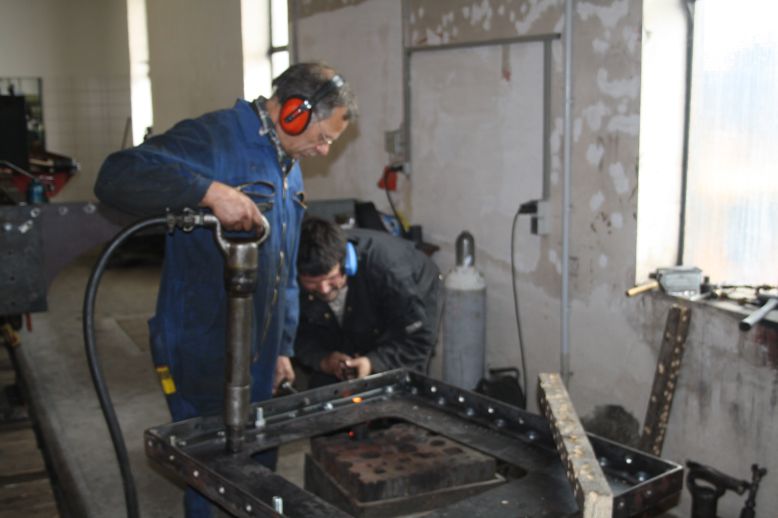
© 2010 Ingo Adam |
Dann muß es schnell gehen, damit der Niet nicht
vorzeitig auskühlt.
Einer steckt den Niet ins Loch und positioniert den Gegenhalter, während
der Zweite schon mit dem Niethammer bereit steht. |
Mit dem pressluftbetriebenen Niethammer wird der Niert
gestaucht und der Kopf geformt. |
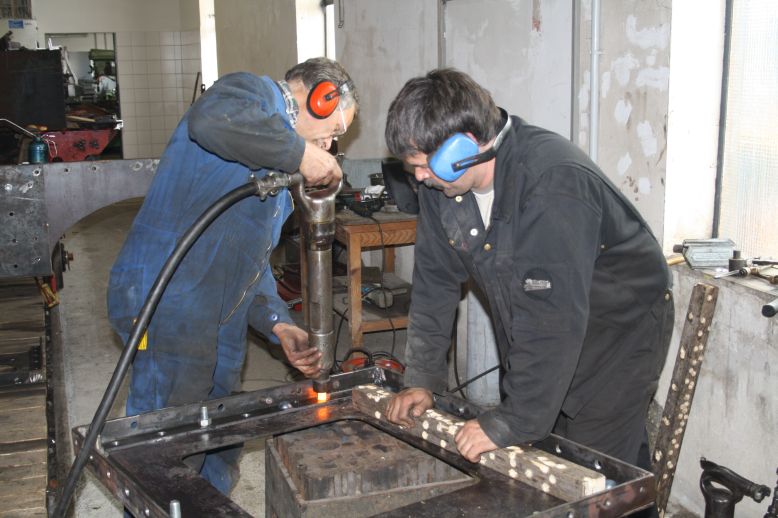
© 2010 Ingo Adam |
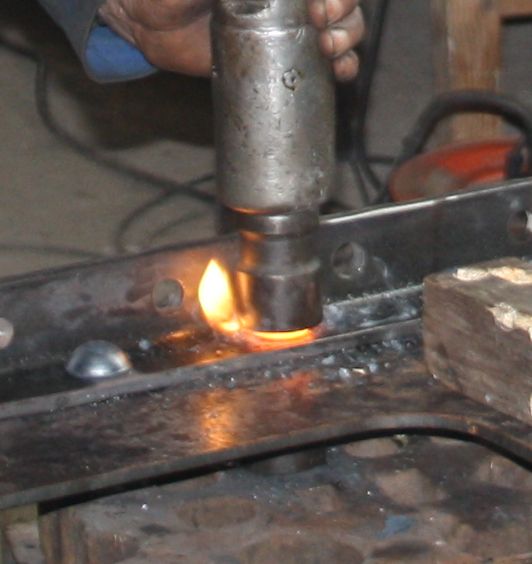
© 2010 Ingo Adam |
Der Kopf ist fast ausgeformt, nur noch wenige Schläge,
dann kann der Niet abkühlen und beim zusammenziehen die genieteten
Teile fest aufeinander pressen.
Dieser Druck, der auch nach hundert Jahren noch vorhanden sein wird, lässt
sich mit Schrauben nicht erreichen. |
[ vorherige Seite ]
[ previous page ]
Copyright © 2010 - 2011 Gerald Stempel,
Gerald.Stempel@t-online.de
[ Letzte Aktualisierung 30.10.2011 Gerald Stempel ]